The Duplication Dilemma
- Anna Davidson
- Jul 10, 2024
- 4 min read
Updated: Jan 19
It’s no secret that every maintenance department has duplication within their MRO Master data set. While some companies have done a great job minimizing duplication through limited user input, strict operating procedures, and defined data standards, others have struggled to address the issue. On average, we see duplicate items range from 15-20% within a given manufacturing site, while the percentage of commonality across multi-site organizations can sometimes range as high as 25-30%. With such high numbers, duplicate items present a major concern that silently leads to inefficiency and unnecessary cost.
So how does this happen and what can we do about it?
Cause of Duplication
As a common challenge that companies face, there is no one person or thing at blame for duplication. When it comes down to it, the main factor that leads to duplication is the fact that multiple people are entering parts. In fact, manufacturing organizations often have multiple sites spread across large geographic regions, each with thousands of spare parts on hand to keep operations running. In such large organizations, several different employees enter items into various software systems at each site. While sheer volume is the main factor, lack of standards and guidelines and the use of multiple languages can also lead to duplication.
For example, imagine employees in different plants are entering a ball bearing. Because of a lack of standardization, they each include the information that they think is important. But when you go back and search for a ball bearing, you might not realize that they’re the same part–or you might not even be able to find them all with your search.

Over time, this lack of standardization causes MRO Master data to become inconsistent, inaccurate and incomplete, resulting in duplicated information.
Effects of Duplication
Why does it matter if there’s duplication in your MRO Master data set? Well, duplication can cost companies thousands, if not millions, of dollars each year. If you can’t find the parts you need, and without delay, you’ll end up with:
Unnecessary maintenance expenses. When you can’t find a part, you may assume you don’t have it and instead pay to buy a new one. Of course, because you’re in a hurry, you may end up paying extra for expedited delivery–not to mention you won’t be able to leverage your spend when buying the part.
Increased equipment downtime. If you can’t find a part easily, the equipment that needs to be repaired or replaced will be down for longer. This alone can cost thousands of dollars in lost revenue, even for a relatively short downtime. Those costs grow exponentially in cases where you cannot find the item at all and instead have to secure a new one.
Increased spot buys. When a part can’t be located because the search you're using isn’t accurate to how it was entered, you’ll likely rebuy the part. This leads to buying at increased prices instead of purchasing in bulk to take advantage of spend leverage.
Incorrectly sized equipment purchases. When you go to do your bulk orders, if your items aren’t standardized, you won’t actually have the proper number for your order. For example, if you’re ordering ball bearings and you see that you used 100 BALL, BEARING, you’ll assume you should order around that amount. However, what you don’t see is the additional 100 BRG BALL in the system that were used. This means you won’t have what you need and will need to do a reorder, and also miss out on the ability to leverage your spend for a better deal.
Inability to leverage warranty. Since warranties only last a set amount of time, you don’t want to have parts sitting around unused well past their warranty expiration. But if parts are entered in different ways, you may not be searching for and locating the oldest parts to use first.
As the item master becomes more and more polluted with duplicate information, equipment downtime and maintenance costs begin to rise, parts cannot be located, false stock-outs occur and maintenance workers scramble to expedite parts, meanwhile there is a perfectly good part sitting on the storeroom shelf. Clearly, this is a problem that needs to be dealt with.
Solution for Duplication
The only solution to remove duplication from legacy data is to implement a data cleansing project. During the cleansing process, legacy data is cleansed, standardized and enhanced to maintain one consistent format and nomenclature. As each unique item is cleansed, it is assigned a Corporate Part Number, which links all items into a “Virtual Warehouse.”
Once the data has been cleansed, standardized and enhanced, duplicate items can then be identified by direct match and fit-form-function similarity. Direct duplicates include two or more items possessing the same manufacturer name, part number and description, whereas fit-form-function duplicates include two or more items that possess different manufacturer names and part numbers, but have the same description.
As duplicates are identified, the Corporate Part Number from the original item is copied down to all of its duplicate records. Using this Corporate Part Number, the duplicate items are now identified and linked across the corporation. A file containing all identified duplicates is then sent to the customer for verification and instruction.
From the sample below, you will notice that the two records originally had different Stock Numbers and inconsistent descriptions. After being identified as direct match duplicates, both records now maintain one consistent description and corporate part number, while the old item numbers remain intact for future reference.
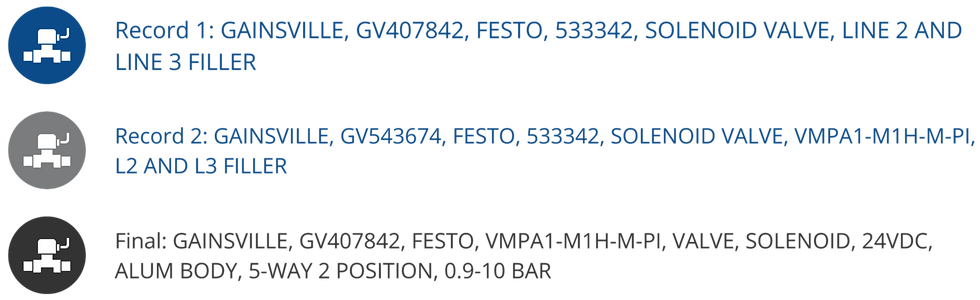
As always, data cleansing can deliver significant cost savings and improved efficiency, especially when it comes to duplicate identification.
How can IMA help?
IMA offers the most customizable option in the industry to cleanse and maintain data. Often, companies struggle to find a proper solution because of their specific schemas and needs. IMA works with you to put the most appropriate solution in place–whether it’s your legacy schema, our proven IMA-developed schema, or something different–so you’ll be confident that you have world class data. And all through the process, we will offer you whatever level of guidance you need!
For more information on IMA and our services, visit www.imaltd.com or contact info@imaltd.com. We’d be happy to chat with you about how we can help!
Kommentare