How MRO Master Data Drives Efficiency: Searchability & Maintenance Efficiency
- Anna Davidson
- Feb 22, 2024
- 6 min read
Updated: Jan 20
This week we’re finishing up our MRO Master Data and Efficiency series with Searchability and Maintenance Efficiency! Make sure to check out our previous blog entries to get the full picture: Overview, Procurement Strategies, and Inventory Optimization.
Why Searchability and Maintenance Efficiency?
First off, why pair these two concepts together? Just like all of the topics we’ve covered, searchability and maintenance efficiency are connected–but these two overlap even more than our other categories. Searchability is key to maintenance efficiency and maintenance efficiency is a main benefit and reason for searchability, which makes it hard to talk about one without the other.
Searchability itself can apply to anyone in your organization, of course. It’s simply being able to access and filter your data so you can better use it–something any department will want to do. For example, your procurement team needs searchable data so that they can better plan purchases. Imagine the difference between making purchases based on feelings or memories versus being able to look at the data of every bearing purchased in the last 12 months so you can leverage spend.
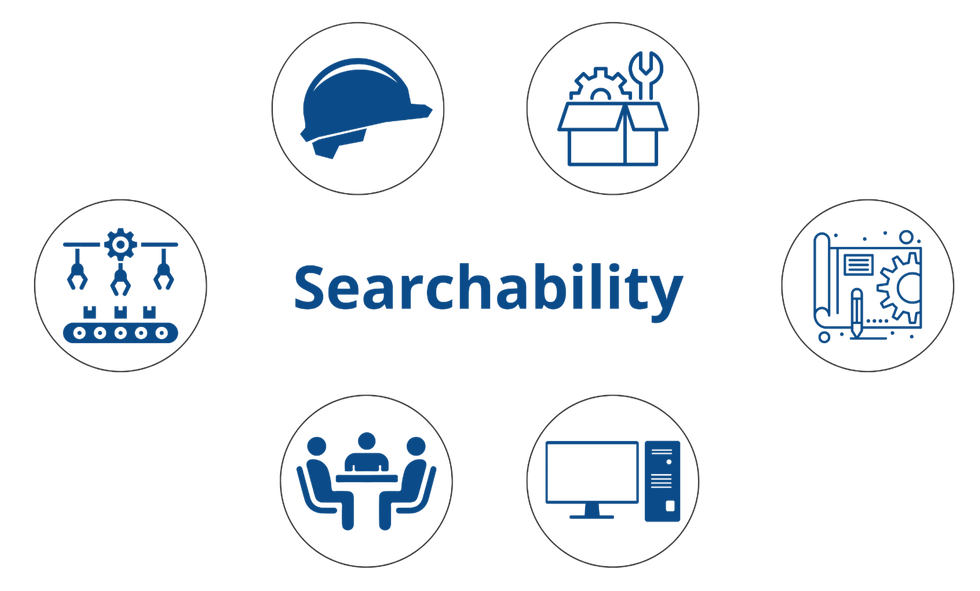
Our main focus in this post, however, is what your maintenance team can do with searchable data. Let’s consider a situation where maintenance needs to find a part; maybe a piece of equipment is broken. The maintenance team searches in the system and doesn’t find anything, so they go to a local supplier to get the part as soon as possible and order two since they don’t want this to happen again. Unfortunately, the part won’t arrive for a few days so the machine is unusable for that period and revenue is lost. Eventually, long after the problem is resolved, you learn that the part was in the storeroom the whole time but the data attached to the item in your system wasn’t consistent with what users actually search on. Because of inconsistent, unsearchable data, the downtime was extended, revenue was lost, and unnecessary parts were purchased.
Maintenance efficiency is about maintenance happening as quickly and seamlessly as possible. That means having planned maintenance in place and being able to search for items for unplanned replacements–both of which require usable data. Essentially, if you can’t find the parts, the repair will be slowed down like in the example above.
Searchability problems
When we discussed searchability before, we identified the following common problems:
Inability to find parts within storeroom
Inability to leverage warranty on stock items
Undue spot buys
Extended equipment downtime
Let’s dive into each of these.
Inability to find parts
This is the most basic problem we see across the industry: a broken search system. If you’re not able to rely on the data you have–or you don’t have accessible inventory data–it makes it hard to anticipate what you’ll find in the storeroom. You may even have the same item stored in multiple different places because they were entered with different data.
Additionally, inventory data is what helps you organize your storeroom and keep it in an order that makes it easy to find parts. So the dilemma is twofold: you need good, consistent data so you can determine what you have without physically looking, and so the storeroom is easily navigable once you’re ready to find the part.
Inability to leverage warranty
Since warranties only last a set amount of time, you don’t want to have parts sitting around unused well past their warranty expiration. In an ideal scenario, you should have a comprehensive understanding of your inventory so that excess parts aren’t kept (leading to a pile up of parts past their warranties) and parts are used in order of oldest to newest. But you can’t do that without having the data available.
Spot buys
We’ve talked about the issue of buying parts unnecessarily and for higher prices in the previous sections of this series–and a lack of searchability is what leads directly to the problem. If you’re unable to find items in your inventory, especially in the face of a catastrophic downtime, you’re likely to go out and buy the item–and spares “just in case”–so you can deal with the immediate issue. Buying outside of contract means you’re likely spending more on the part than you otherwise would and aren’t able to leverage spend.
Equipment downtimes
Being able to find the parts you have (or identify what you don’t have) can be make or break when it comes to downtimes. If you can easily search for the item, then you might save hours or even days of downtime. If this sounds familiar, it’s because searchability ties heavily into inventory optimization–everything is interconnected!
Maintenance efficiency problems
In our introduction blog post, we outlined the major issues in maintenance efficiency as:
Stock duplication
Unnecessary spot buys
Poor maintenance history tracking–which continues the cycle of poor efficiency
Inability to develop an effective preventative maintenance schedule
What do these really mean?
Stock duplication
Without a consistent approach to data entry and cleansing, you likely have items being entered differently in multiple places. After all, everyone looks at things differently and identifies different pieces of data that they think are important. Imagine all the different ways you could enter the same ball bearing.

Duplicate entries create problems for your maintenance team, though. If they’re unable to find a part when they search for it because the data isn’t what they expect, they’re going to spot buy that part rather than wasting time looking for something they assume isn’t there. That can mean a delay in the repair, whether it’s hours or days, and money spent on something you already have in the store room.
Spot buys
As we discussed in the section above, spot buys are a problem because you’re likely paying more than you should for an item from a non-preferred vendor instead of bulk ordering to leverage spend. If you’re not properly prepared for maintenance with the right amount of parts in storage, or your parts are not able to be found, then you have to value urgency over cost efficiency. You buy the part because it will save you from excess downtime, even though you may have one already (or because you didn’t properly consider how many parts you would need for maintenance yearly and didn’t have it at all).
Preventative maintenance schedule
Developing a preventative maintenance program is an incredibly important step in reducing downtime and chances of catastrophic failure. Essentially, the program is a schedule you can follow to perform regular maintenance so you can keep equipment running in good condition–the same way you change the oil in your car regularly rather than letting the engine break before you take it in. Doing regular activities like swapping out a belt every six months can prevent unplanned downtime and lost revenue. However, you can’t hope to set up a preventative maintenance program without having the data to do so and the means to continue entering and tracking that data. Without that data, you have to rely on fixing problems when they arise instead of being prepared.
Maintenance history tracking
To develop a preventative maintenance program, one piece of the puzzle you need is your maintenance history. The first thing to do when analyzing your maintenance or creating such a program is to call up the history of repairs on the piece of equipment to see what has failed on it, what the frequency of failure is, and so on. If the data lacks in quality, you won’t be able to identify how many times you’ve had to repair it or what you’ve had to repair, and without that data you can’t plan for the future.
What can you do to improve searchability and maintenance efficiency?
Both searchability and maintenance efficiency come down to data. You need the right data, readily available to make it possible to easily search your parts–that improved part availability results in faster equipment repair times and more effective planned maintenance.
So what data do you need? First of all, your MRO Master data needs to be standardized and cleansed to a consistent schema. There are a variety of different ways to do so–different schemas to use, different ERPs to connect to, and so on. It’s also important to have ongoing governance of the data so your efforts aren’t a one time project that quickly gets forgotten. You can learn more about the cleansing process here.

Maintenance history data is also invaluable for your maintenance team’s efficiency and the ability to put plans in place for the future. That means you need to collect this data uniformly and determine strategies to search, analyze and use it.
What are the benefits?
Clean, usable data leads to being able to search your data properly. That searchability means you can:
Find parts faster
Avoid duplication and spot buys that come from not being able to find the part you need
Set up preventative maintenance programs
Better service your equipment and avoid downtime
Set up maintenance reminders
Ultimately, data harmonization saves your maintenance team time and resources, which means revenue savings.
So what do I do next?
Are you stuck, unsure of how your organization can take advantage of your data for searchability and maintenance efficiency? IMA has decades of experience in data cleansing and governance–and assisting our clients in optimizing their data. Contact us at info@imaltd.com for more information about how we can help you with your data goals.
You’ve reached the end…
This ends our series on how MRO Master data drives efficiency! Of course, there are plenty of other areas that your MRO Master data affects and we’ll certainly talk about more of those in the future. If you have any comments or topics you’d like to see us discuss next, contact marketing@imaltd.com! We’re always interested in what you have to say, and eager to explore your interests here on our blog.
Comments